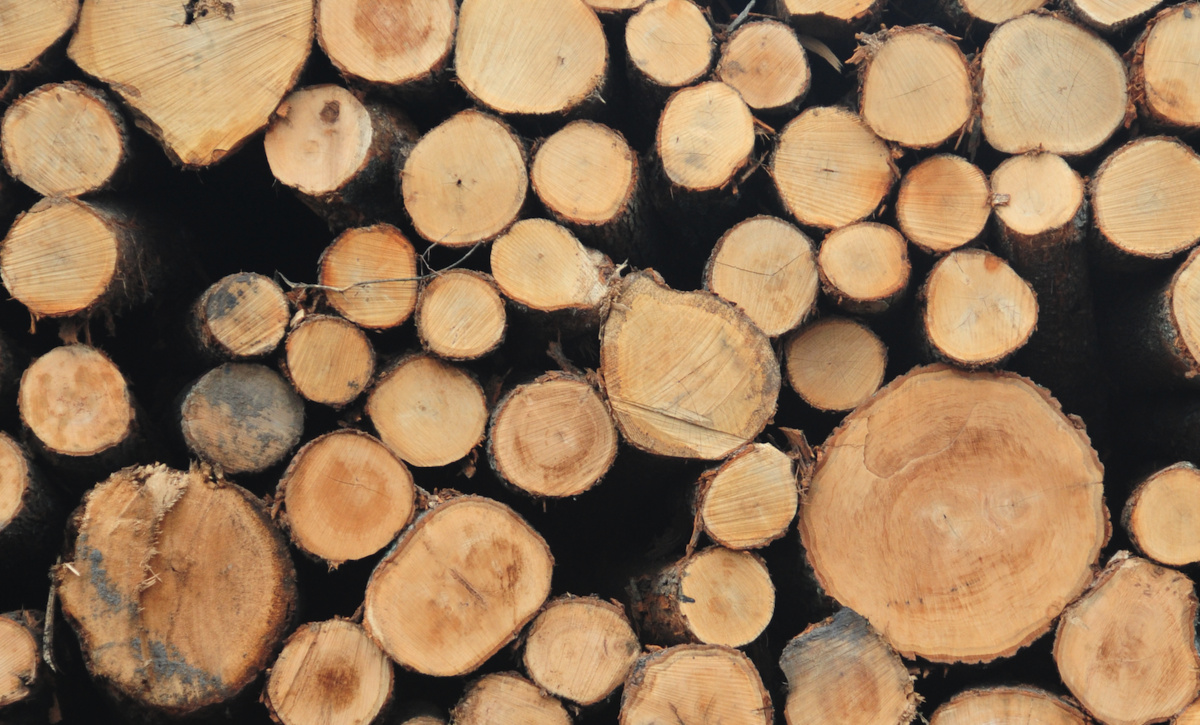
There's Gold in Our Timber
Can northern Michigan handle it?
By Todd VanSickle | May 22, 2021
You’ve probably seen the high demand for lumber and its skyrocketing prices of late. Or maybe, like folks driving along M-72 between Williamsburg and Grayling in the last year, you noticed a large swath of forest has vanished. With mega South American company Arauco’s opening of a giant plant in Grayling in 2018, and Michigan Lumber and Wood Fiber Inc. of Comins, Michigan constructing a state-of-the-art sawmill on Georgia Pacific’s old campus near Gaylord this year, and local lumber retailers pricing their supply higher and higher we had to wonder: Is there a timber boom on? And if so, can northern Michigan handle it? Northern Express looks into the state of the state’s forest industry — home to more than 1/3 of manufacturing jobs in the U.P. and, at last count, driving $891 million into the state’s economy from U.P. and northern Lower Michigan alone.
AJD Forest Products, located just south of Grayling, vibrates with activity from 6am to 3:30pm five days a week. Outside the mill, the buzzing saws and the rumbling of heavy machinery carrying large logs to be debarked resonate throughout the body while the smell of freshly cut wood hangs in the air. Inside the facility, a host of workers sort through rough-cut hardwood boards of varying lengths zipping along conveyor belts high and low. At the end of the line, the boards are bundled, stacked, and loaded onto tractor-trailers and shipped out to customers or kilns to be dried.
The facility is busy, but in one corner of the building, a machine that was installed during the height of the pandemic sits idle.
“We don’t have enough workers,” AJD General Manager Tim Neff said. “If we had the workers here, this machine would be running.”
As pandemic restrictions ease and businesses re-open, lumber orders are returning to normal, but prices are skyrocketing, especially for soft lumber like pine.
In 2019, a 2-by-4 stud commonly used in building was priced around $5 a board. Now, the price is twice as much — and it continues to increase.
Lumber prices are up 67 percent since January and up 340 percent from a year ago, according to Random Lengths, a wood-products-industry tracking firm. It is estimated that the price increase has added more than $35,000 to the price of an average new single-family home and almost $13,000 to the market value of an average new multi-family home, according to the National Association of Home Builders.
Perhaps not surprisingly, the rising lumber prices have made such an impact, cut wood has achieved a near Kardashian-level fame as Internet-meme fodder. Images of small bags of sawdust selling for $1.2 million aside, the actual but still exorbitant prices for lumber are no laughing matter for homebuilders.
John Packard, who was shopping at Home Depot in Traverse City in April, told Northern Express he’d had plans to build a small home on a piece of property in Kalkaska, but lumber prices impelled him to postpone.
“It is going to cost me more, like $20,000 more, just in lumber,” he said. “I think I’ll wait until things return to normal.”
MANY TREES, TOO FEW LABORERS
Will prices return to normal, however? That depends on who you’re asking, and where they place the blame. Some experts point to low interest rates and a booming housing market for the rising prices.
Neff says the lumber industry sees a different culprit: a broken supply chain and sheer lack of workers.
“That supply chain, if it’s empty, takes a long time to fill it up, and that's where we're at now,” Neff said. “It was pretty depleted.”
During the start of the pandemic, some sawmills and logging operations, especially in the southern United States, were not deemed essential. Meanwhile, more and more people were unemployed or working from home and taking on home-improvement projects like building decks and other renovations. The demand for lumber went up, but the supply wasn’t being replenished at the same rate. The uncertainty forced retailers to cut back on orders.
Orders at AJD — which mainly focuses on hardwood species like red oak — fell by more than 80 percent.
“April of last year we were staring at a pretty bleak situation,” Neff said.
Before April, however, AJD’s production had been on track for a record-breaking year.
“We'd had a great production year in 2019,” Neff said. “And we were running ahead of that production rate for the first three months of 2020. And then, the pandemic hit, and we ended the year, like, 75 percent of what we would expect.”
Neff described the situation as something they had to navigate week to week, but said the company forged on and continued to fill orders with whatever inventory they had in the yard. The production manager said the company didn’t have any layoffs but did trim the schedule to 32-hour weeks, with employees taking one day of unemployment, instead of their normal 45-hour workweeks.
“It was better than nothing,” Neff said.
The company began rebounding around November and is now almost at full capacity. In fact, employees are now working overtime, and AJD is looking for a handful of new employees.
“The additional people would allow us to put more production through the mill by running saws that are idle today,” Neff said.
If the facility were able to run at full production, even some of the positions currently filled — such as truck driver — could expand to add more employees in those roles.
That’s a big “if,” however. Although ADJ offers competitive wages and benefits, the production manager said he’s finding it hard to find employees. Mainly, because so many other companies are trying to hire, too — not only other sawmills but various businesses, like restaurants and stores. He added that extended unemployment benefits have also hampered their hiring process.
AJD employs 50 full-time workers and contracts about six private logging operations that have numerous employees.
One of Neff’s main concerns is having enough people to run the mill.
“If we didn't have orders, the worry would be orders — well, we've got orders to be running at full capacity,” Neff said. “But we can't run at full capacity, because we don't have enough people.”
Complicating matters: Many customers are now doubling their orders, Neff said.
“From our industrial lumber customers, when they place an order, what we're used to seeing, they are now doubling that,” Neff said. “And it's only double that because everybody wants to be in the queue sooner.”
The wait time is not only affecting the lumber but everything else is taking longer to reach its destination.
“Outside of logs, everything we order has a longer lead time to get it here than it had before the pandemic,” Neff said. “Saws that we used to order might take three to four weeks, now it’s an eight- to ten-week wait.”
Since 1979, the company has sourced timber within a 100-mile radius of its facility. Neff said there is an ample supply of lumber in Northern Michigan.
A CAREFUL BALANCE
“The log supply will be there,” Neff said. “The standing timber is actually growing faster than it's being harvested, and it has for years and years. The concern gets into if it's not a working forest — if it’s not a managed forest.”
The production manager said AJD works closely with the Department of Natural Resources Forestry unit to ensure sustainability.
Dave Neumann, of the Department of Natural Resources, is a forest market and utilization specialist. He said the DNR manages about 4.1 million acres of forestland and puts up 55,000 acres of timber for sale each year.
“But last year, I think we struggled to make 50,000 acres available for sale, because of the restrictions and the health and safety guidelines of the governor’s executive orders,” Neumann said. “We weren't able to go to work in the offices all of last year, except in very limited circumstances. Many of our staff was working from home. We were able to put up timber, but we had to be very careful to keep workers safe — and the public safe — during that process so that had an impact on our ability to put up timber for sale.”
The stands are put up for auction and the winning bidders have two to three years to harvest the timber.
The revenue from timber sales goes back into the forest development fund, which is used for preparing additional timber sales and managing state forest activities, including wildlife habitat.
Neumann spent seven years of his DNR career as a silviculturist, a specialist position in Lansing that focuses on forest management and providing guidance on how to grow trees.
“We reforest about 5,000 acres a year,” Neumann said. “We end up planting about five million seeds a year. But not last year — we struggled to plant three million because of the impacts of the pandemic.”
The majority of the timber that is harvested does not need to be replanted, he added. The majority of it, like oaks, maples, and beeches regenerate naturally from seed or from sprouts. However, 95 percent of conifer species, like red and jack pines, are replanted. The difference is noticeable when loggers harvest an area: A pine plantation is almost clear-cut while a hardwood forest is thinned out.
It takes about two to three years from the time a timber stand is harvested to when the trees are replanted, according to Neumann.
The DNR’s forest management ensures that the timber industry remains sustainable on public lands. However, 70 percent of the forestlands in Michigan are privately owned and there is no forest practice legislation or requirements for landowners when it comes to logging. The fate of the land and trees is left up to the private landowner.
On occasion, AJD gets complaints from adjacent landowners about logging operations, but says they follow the guidelines and prescription handed down by the DNR.
“It's more a visual complaint, because most of the land is being managed for sustainability. So, that's not a big issue; it's the optics, the visual impact,” Neff said.
The DNR forest specialist reaffirmed the department’s commitment to sustainability.
“We are certified on our two forest certification systems, both of which require that we document and maintain prompt reforestation and we are in compliance with sustainability,” Neumann said. “The No. 1 criteria is that we don't harvest more than we are currently growing. There's not much risk that the state forest land that is administered by the DNR is going to run out of timber. There’s a positive outlook for the forest products industry in Michigan.”
The forest products industry makes up about five percent of all manufacturing jobs in the state but is a much more important employer in the Upper Peninsula, where it accounts for 30 percent of all manufacturing jobs.
“The forest products industry is important — more important in rural areas than urban areas,” Neumann said.
Neff, too, is optimistic about the future of the logging industry in Northern Michigan, but is knocking on wood in hopes that AJD will soon get the employees they need.
“The company's been around long enough that we know there's ups and downs,” Neff said. “The important thing is to keep your technology up to date and improve it when you can. And don't be overextended so you can get through the rougher stretches of the economy.”
RISING FROM THE ASHES & AUTOMATING
Tim Bills is the owner of Michigan Lumber and Wood Fiber in Mio. A couple of years ago the company’s sawmill was lost to a “catastrophic” fire, the owner said. Currently, he is in the process of rebuilding the mill, but in the meantime, the company has stayed active in the lumber industry.
“I buy standing timber, and I have logging, chipping crews, and log trucks,” Bills said. “I sell to other sawmills while mine is under construction and being rebuilt.”
All throughout the pandemic, Bills says his company has remained busy and hasn’t seen a slowdown. He buys standing timber, mostly hardwood, from both public and private landowners. In spite of rising lumber costs, he hasn’t seen an influx of private landowners wanting to sell their trees.
“I am not really seeing a flood of landowners reaching out to us wanting to sell their timber. Right now, it’s got national attention because of the price of it,” Bills said. “You would think landowners would be wise to it and would be reaching out and trying to sell their timber, but we’re not getting overwhelmed.”
Bills said when private landowners have their property logged, he gets a variety of requests. His company provides consultation and gives advice based on the property owner’s goals.
“You have people that may inherit the land and then they just want to get all the money they can out of it,” Bills said. “We'll still go in and give our recommendation for the proper way to manage the forest and how to harvest. And sometimes, people just don't care. They just want all the trees cut. They want to get all the money they can, and that's certainly their right to do so. But, again, we will always try and coach them into the best forestry practices that are sustainable and healthy.”
He says hasn’t seen a bigger demand from sawmills to cut down more conifers despite the rising prices.
Bills first got into the business when he was 19 years old when he bought a semi-truck to haul wood. Over the past 30 years, he has had a hand in many aspects of the business. At one point when his sawmill was operational, he employed about 70 workers, with a competitive wage and benefits, he said. However, he doesn’t see the company having as many employees in the future. He plans to automate the operation as much as possible because maintaining a large staff and getting people to work five days a week has been too challenging.
“We were a very profitable operation then, but it was appalling trying to get people to come to work,” Bills said, who expects one of his sawmills back up and running in the next couple of weeks.
Being in the lumber industry in Northern Michigan is very advantageous to stakeholders like Michigan Lumber and Wood Fiber and AJD, who both sell wood chips to Arauco, which produces composite panels, plywood, millwork, and lumber and wood pulp to companies like Sauder Woodworking.
Arauco operates multiple production facilities in both North and South America and ships to more than 3,500 destinations throughout North America. The company opened its Grayling facility in April of 2019. The $450 million plant is a 820,000-square-foot facility that staffs more than 200 full-time employees and houses North America’s largest-capacity, continuous single-line particleboard press. The mill has a total production capacity of 452 million square feet on a 3/4-inch basis, according to www.woodworkingnetwork.com. The company did not respond to multiple interview requests for this story.
If other companies in the region are any indication, it’s likely Arauco is also enjoying the present market. “They didn't come here and build that plant on a wing and a prayer and hope that there's enough trees to support it for five years,” Bills said.
Other companies in the area also make it more profitable for logging and sawmill operations, including the Grayling Generating Station, the Cadillac power plant, Weyerhaeuser, and Georgia Pacific, to name a few.
“There's probably no better place in the world right now to be in the logging and lumbering sawmill business than in northern lower Michigan,” Bills said. “We got outlets for our percent utilization for trees. Nothing goes to waste.”
Great Lakes Tissue
From a 2008 bankruptcy to a 2020 pandemic boom to a 2021 slowdown, Cheboygan’s family-owned recycled paper company presses on
Great Lakes Tissue could not produce enough of their paper products during the start of the pandemic.
But now the company is struggling.
“Right now the paper industry is taking a hit,” said Great Lakes Tissue Team Leader Gary Loftin. “It’s not only us, but all the paper companies. They are having a hard time moving product.”
He attributes the downturn to people “bulk buying” and many businesses closing or limiting hours.
The company makes only two products: paper towels and toilet paper. Some of Great Lakes Tissue’s main customers are schools, colleges, and offices.
“The boom actually killed us,” Loftin said. “We did good during the boom, but we are struggling.”
Normally, the company would produce about 350 tons of paper in a week. But now they have had to cut back to about 150 to 200 tons per week.
Fortunately, the company has not had any layoffs, which Loftin credits the owner for his “loyalty to the employees and community.” However, hours have been cut back.
“We aren’t getting what we used to, but we are surviving,” Loftin said, who has worked for the company for 15 years.
One cost-effective move the company made was done long before the pandemic.
The company made the transition from wood to recyclable paper about 25 years ago.
“All that [paper-making] equipment has been gone for at least 20 years,” Loftin said.
Great Lakes Tissue has a partnership with companies in Ohio and Canada that send them paper products that would be destined for a landfill. All of their products are made from recyclable scrap paper.
“We run no wood pulp,” Loftin said. “Everything is recyclable.”
The team leader said making the move away from wood has benefited the company, especially with today’s rising cost of wood.
“The cost of making paper from wood pulp is a lot higher,” Loftin said.
Additionally, when Cheboygan lost the local train, it became a matter of logistics, he said.
Despite the obstacles, Loftin is optimistic that paper production will rebound.
“For us, it is going to take the country opening back up, which it is doing now,” Loftin said.
Trending
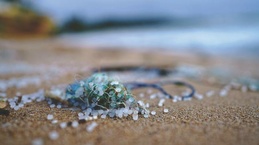
Microplastics Are Everywhere, But Local Organizations Are Fighting Back
At a glance, Michigan’s lakes, rivers, and streams look healthy. However, a quirk of human psychology is such that whi… Read More >>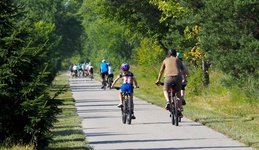
A Weekend for Cyclists
Two big biking events roll through northern Michigan this weekend. Friday, July 18, TART Trails celebrates the Tour de TART,… Read More >>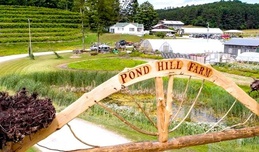
Pond Hill Turns 30!
Pond Hill Farm does a little bit of everything. It’s a brewery and a winery. A cafe and a market. A pizza joint and a … Read More >>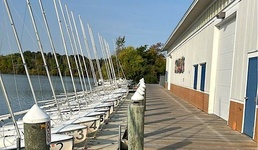